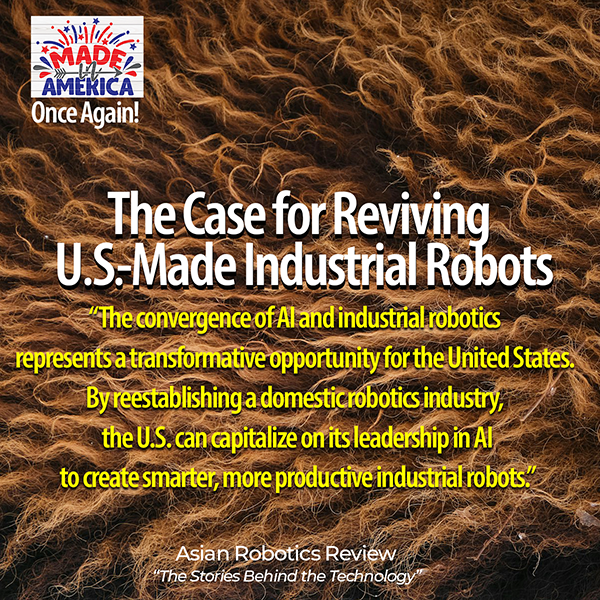
Once Upon a Time in America
Should the U.S. Make Its Own Industrial Robots...
Again?
“The convergence of AI and industrial robotics represents a transformative opportunity for the United States. By reestablishing a domestic robotics industry, the U.S. can capitalize on its leadership in AI to create smarter, more productive industrial robots.”
“I have a foreboding of an America in my children’s or grandchildren’s time — when the United States is a service and information economy; when nearly all the manufacturing industries have slipped away to other countries…” —Carl Sagan
Prologue: The Why of It All
Once upon a time in America, there were nearly fifty domestic makers of industrial robots. One of them, the high-flying Cincinnati Milacron Inc., the nation’s leading machine tool manufacturer, was closing in on its goal of becoming the No. 1 company in the booming market for industrial robots. A 1973 NYT’s headline blared: “Milicron’s Goal: No. 1 in Robots. James A.D. Geier, president and chief executive officer of Milacron, expects to continue ”traveling faster than our rivals.”
That was in 1973. By 1983, most of America’s domestic industrial robot manufacturers were either dead or moribund. Congress was unnerved over the losses and demanded answers from United States International Trade Commission. What Congress got Competitive Position of U.S. Producers of Robotics In Domestic and World Markets (1983) was far from pretty.
The why of it all, claimed the report was that the industry suffered from three mortal blows: “The recession of 1979-1982; attended by ‘largely non-existent’ government funding; and foreign imports aggressively jumping from $3.8 million in 1979 to $28.9 million in 1983.”
America’s robot industry, built upon American George Davol’s 1954 patent for a robotic arm, which became the Unimate, the world’s first industrial robot, and then in 1973, with Milicron’s ‘The Tomorrow Tool’ or T3, the world’s first “commercially available computer-controlled industrial robot,” was virtually dead as a leading American industry, yet a burgeoning one for many foreign manufacturers.
Adept Technology was the last holdout of U.S. manufacturers of industrial robots, and it succumbed in 2015, acquired by Omron (Japan). Today there are ZERO U.S. manufacturers. The Swiss/Swedish ABB manufacturers industrial robots in its Auburn Hills, Michigan plant; other than ABB, U.S.-based foreign companies merely “assemble for sale” from robot parts manufactured offshore.
From our 2018 article on industrial robots in North America; a bit dated but still highly relevant.
The 2017 WSJ article, Foreign Robots Invade American Factory Floors, concluded: “In the 1980s, as U.S. manufacturing slumped [the aforementioned 1979-1982 recession], almost seven of 10 American machine‐tool companies closed due to falling demand, the strong dollar and strategic miscues. The decline continued this century as U.S. manufacturers outsourced more and baby boomers retired. Shrunken manufacturers demanded fewer production experts, accelerating the factory‐technology decline.”
Of course, all of that was once upon a time in America. The $28.9 million from 1983 has now ballooned some forty years later, according to Grand View Research, to an estimated $2.17 billion in 2023 with a CAGR of 5.4% through to 2030. Interestingly, the foreign manufacturers deploying industrial robots in the U.S. do so in predominantly five states in the Mid-west, states referred to by the Chicago Federal Reserve as “automobile alley”: Iowa, Michigan, Kansas, Wisconsin, and Minnesota.
Authors of a recent Stanford study, The Characteristics and Geographic Distribution of Robot Hubs in US Manufacturing Establishments, remarked in surprise, “For now, the striking finding was how concentrated the robots are.” The study notes that 77% of all industrial robots are sold into these five states, that’s more than 7 out of every 10 industrial robots sold. In short, a very heavy concentration.
It appears that vendor sales efforts are heavily weighted to the automobile industry, the traditional cash cow of industrial robotics going back to the Unimate days of the 1960s. When “automobile alley” is flying high, so are industrial robot sales, as they were in 2022; in times of trouble with the auto industry, as was 2023, industrial robot sales tumble. The conjecture here is that industrial robot and cobot vendors prefer catering to what might be termed the low-hanging fruit of the traditional auto industry. The assumption being that the other 45 states are not nearly as well served because the five robot hubs are purposely over-served.
More importantly, the new report also sheds light on the fact that “Robot-adopting firms can gain market share and potentially displace less productive non-robot-using firms.” In other words, factories that are not automated can’t compete with those that are; and those currently getting “outproduced” are thus in jeopardy of going under. For non-Robot Hub states that’s bad news.
But that’s exactly what is happening, especially with SMEs (small to medium manufacturing enterprises, which are those with 499 or fewer employees). Such a contraction among SMEs is underway and borne out in MIT’s Manufacturing in America: A View from the Field.
This five-state concentration of efforts by foreign manufacturers adversely affects SMEs in non-hub states, and therefore, adversely affects manufacturing productivity in the U.S.
With SME’s representing 94% of America’s manufacturing establishments, and with fewer than 10% of these SMEs having any robot automation at all, and with five states receiving the lion’s share of industrial robots, America may be looking at the perfect storm of events and conditions to revive domestic robot production and to democratize the spread of industrial robots to all fifty states, and not just to the Big Five!
Added to that potent possibility is America’s current leadership role in artificial intelligence, in general, and specifically, GenAI’s convergence with industrial robots.
This may well be the perfect opportunity to revive America’s domestic industrial robot industry. To that end and to visualize what it might mean, we have put together a scenario, that we call: The Case for Reviving U.S.-Made Industrial Robots
The Case for Reviving U.S.-Made Industrial Robots
The United States has long been recognized as a global leader in innovation, particularly in artificial intelligence (AI) and generative AI (GenAI).
However, when it comes to industrial robotics, the U.S. has ceded ground to foreign competitors. Today, approximately thirty thousand industrial robots are annually provided by foreign manufacturers to United States, primarily from Japanese manufacturers. With advancements in AI making robots smarter and more efficient, the convergence of GenAI and industrial robotics presents a pivotal opportunity for the United States to reenter the industrial robot manufacturing space. The strategic, economic, and technological benefits of producing domestically designed and manufactured industrial robots are compelling.
ECONOMIC BENEFITS
Job Creation and Economic Growth Revitalizing the domestic industrial robotics industry would create a cascade of economic benefits. Manufacturing industrial robots in the U.S. would generate high-skilled jobs, ranging from engineering and software development to assembly and quality assurance. The supply chain for industrial robot production could also stimulate ancillary industries, including precision machining, electronics, and materials science.
Moreover, fostering a domestic robotics industry would boost regional economies. Advanced manufacturing hubs could emerge, particularly in areas with a history of industrial activity, such as the Midwest. This regional growth would help reduce economic disparities and fortify local economies.
Reducing Trade Deficits By importing tens of thousands of industrial robots annually, the U.S. contributes to its trade deficit. Producing these robots domestically would not only retain capital within the country but could also position the U.S. as an exporter of cutting-edge robotics technology. This shift could strengthen the nation’s economic resilience and improve its trade balance.
TECHNOLOGICAL ADVANCEMENTS
Synergy with AI Leadership The convergence of AI and robotics represents a transformative moment in technology. The U.S.’s leadership in AI—including advancements in machine learning, computer vision, and natural language processing—provides a significant advantage in designing next-generation industrial robots. By integrating GenAI capabilities, domestically produced robots could achieve unparalleled levels of intelligence and adaptability, enabling them to perform complex tasks with minimal human intervention.
Fostering Innovation A robust domestic robotics industry would serve as a catalyst for innovation. Collaboration between academia, private companies, and government agencies could accelerate breakthroughs in areas such as human-robot interaction, autonomous decision-making, and energy efficiency. Furthermore, a vibrant robotics ecosystem would attract top talent and encourage entrepreneurship, creating a virtuous cycle of innovation.
NATIONAL SECURITY AND SUPPLY CHAIN RESILIENCE
Reducing Dependence on Foreign Manufacturers The U.S.’s reliance on imported industrial robots poses risks to national security and economic stability. In times of geopolitical tension or supply chain disruptions, access to critical technologies could be compromised. By manufacturing industrial robots domestically, the U.S. would mitigate these risks and ensure the availability of essential technologies.
Enhancing Strategic Capabilities Industrial robots play a critical role in sectors such as aerospace, defense, and advanced manufacturing. Developing a domestic robotics industry would enhance the U.S.’s strategic capabilities, enabling it to maintain a technological edge in these vital areas. Additionally, domestic production would ensure compliance with stringent cybersecurity standards, reducing the risk of intellectual property theft or malicious interference.
ENVIRONMENTAL SUSTAINABILITY
Reducing Carbon Footprints Manufacturing industrial robots domestically would reduce the environmental impact associated with international shipping and logistics. Shortening supply chains would decrease greenhouse gas emissions and contribute to global sustainability goals. Furthermore, U.S.-based manufacturers could implement environmentally friendly practices, such as using renewable energy and recycling materials, to further minimize their ecological footprint.
Advancing Green Technologies A domestic robotics industry could also contribute to the development of green technologies. For example, robots designed for renewable energy sectors—such as solar panel installation or wind turbine maintenance—could accelerate the transition to a sustainable energy future. By integrating GenAI, these robots could optimize efficiency and reduce waste, further amplifying their environmental benefits.
COMPETITIVE ADVANTAGE IN THE GLOBAL MARKET
Establishing Leadership in Next-Generation Robotics The integration of GenAI with industrial robotics is poised to redefine the global robotics landscape. By leveraging its strengths in AI, the U.S. has the potential to become a leader in next-generation robotics. Domestically manufactured robots could set new standards for intelligence, reliability, and adaptability, giving U.S. companies a competitive edge in the global market.
Capturing Emerging Markets As industries worldwide adopt automation to enhance productivity and address labor shortages, the demand for advanced industrial robots is expected to grow. By reestablishing a domestic robotics industry, the U.S. could capture a significant share of this expanding market. Emerging economies, in particular, represent a promising opportunity for U.S.-made robotics solutions.
POLICY RECOMMENDATIONS
To realize the vision of a revitalized domestic robotics industry, a coordinated effort is required from government, industry, and academia. Key policy recommendations include:
- Incentivizing Investment The government should provide tax incentives, grants, and low-interest loans to encourage investment in robotics manufacturing. Public-private partnerships could also play a vital role in funding research and development.
- Supporting Workforce Development A skilled workforce is essential for a thriving robotics industry. Educational initiatives, such as STEM programs, vocational training, and apprenticeships, should be expanded to equip workers with the necessary skills.
- Promoting Research and Collaboration Increased funding for robotics research, particularly in areas like GenAI integration and human-robot collaboration, would accelerate innovation. Collaboration between universities, research institutions, and industry players should be encouraged to foster a dynamic ecosystem.
- Strengthening Trade Policies Trade policies should prioritize the competitiveness of U.S. robotics manufacturers. Measures such as tariffs on imported robots or subsidies for domestic producers could help level the playing field.
CONCLUSION
The convergence of AI and industrial robotics represents a transformative opportunity for the United States. By reestablishing a domestic robotics industry, the U.S. can capitalize on its leadership in AI to create smarter, more productive industrial robots. The benefits—ranging from economic growth and technological innovation to national security and environmental sustainability—make a compelling case for action. With strategic investments and coordinated efforts, the U.S. can reclaim its position as a leader in industrial robotics, driving progress and prosperity in the 21st century.