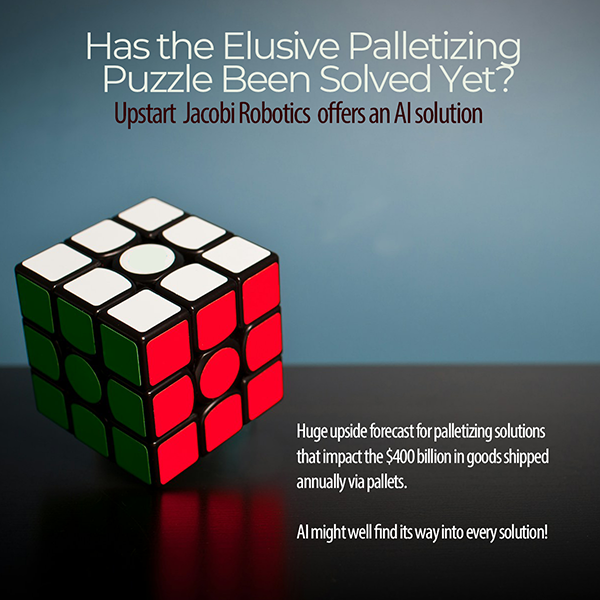
AI Converges
With the Puzzle of Palletizing
Jacobi Robotics showing AI-enhanced solutions as the future standard for palletizing/depalletizing worldwide
that have changed little since the 1980s.” -MIT Technology Review
AI comes to palletizing
With more than 2 billion pallets loaded with goods sliding along the globe’s supply chains, it’s amazing to think that billions of dollars’ worth of American goods are annually packed atop their slim wooden frames for transport. Actually, that number has been reckoned to be about $400 billion a year.
Artfully and safely stacking goods on pallets for shipment has been going on for nearly a hundred years by both humans and machines. Particularly for robots and their developers, a winning solution could well mean mega-sales orders for robots/cobots to palletize and depalletize a fat chunk of that $400 billion.
To date, palletizing robots have only thinly penetrated the massive market potential worldwide. For example, in 2024 the palletizing robot market was barely $3.23 billion; and 2028 is projected to be a little shy of $5 billion. With a palletizing cell averaging $150,000, that means about 23,000 or so palletizing solutions have been deployed this year, which is a small fraction of world robot production. FANUC’s Japan-based robot plants, for example, alone output 8,000 robots a month.
In addition, Future Market Insights reports that another of the factors restraining the growth in palletizing robots is that in most cases, costly programmers must reprogram automated palletizing systems when product sizes or production processes are changed, changes which happen often in today’s manufacturing industry. Multi-millions of dollars have been spent by developers like Universal Robots, FANUC, ABB, KUKA, Techman, Doosan Robotics, Omron, Staubli, and a half-dozen others, who are vying for leadership in palletizing by offering their own proprietary solutions.
These days, with GenAI converging with robots everywhere and seemingly for every possible job, vendors are beginning to add AI to their own palletizing offerings.
Jacobi Robotics, with a slim $5 million in VC money, is out offering its own AI-converged solution that just may prove to be a big winner.
Path planning
The key to any palletizing solution is something called “path planning,” which is all about picking up a carton or box and getting it palletized by the best route. Over the last few years, a sort of pallet war has broken out among robot vendors, with some announcing victory over path planning with their various palletizing solutions.
Nay, nay, not so fast, says newbie Jacobi Robotics, which claims that it alone has the best AI-enhanced, path-planning resolution to the palletizing puzzle.
Emeryville, CA-based Jacobi Robotics was founded in 2022 by four UC Berkeley students. Their professor, Ken Goldberg, serves as the company’s chief scientist. Goldberg also co-founded a package sorting robotics company Ambi Robotics…another process where path planning reigns supreme.
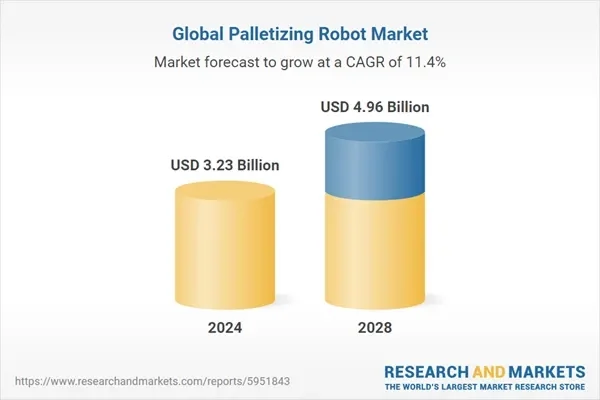
Goodbye teach pendants
“In repetitive tasks, where the robot follows the same motions repeatedly and blindly, robots must be programmed to avoid path planning problems through weeks of tedious manual fine-tuning of robot paths. In addition, for many robot applications, the robot paths must be modified periodically due to small changes in materials or thermal expansion.”
Jacobi Robotics says that it’s “bringing a modern software development framework to industrial robotics by leveraging recent breakthroughs in motion planning from UC Berkeley’s BAIR (Berkeley Artificial Intelligence Research) Lab.” Jacobi claims its platform helps “businesses develop and deploy intelligent robot arm solutions in dynamic environments faster.”
A recent MIT Technology Review article explains the Jacobi process as one that “aims to replace the legacy methods customers are currently using to train their bots. In the conventional approach, robots are programmed using tools called “teaching pendants,” and customers usually have to manually guide the robot to demonstrate how to pick up each individual box and place it on the pallet. The entire coding process can take months. Jacobi says its AI-driven solution promises to cut that time down to a day and can compute motions in less than a millisecond.
After much trial and error, reported Jacobi’s founders…they claim they’ve solved the palletizing puzzle. Their software, built upon research from a paper they published in Science Robotics in 2020, uses deep learning to generate a “first draft” of how an arm might move an item onto the pallet. Then it uses more traditional robotics methods, like optimization, to check whether the movement can be done safely and without glitches.”
Glitches, in robotics, often refer to blockages or singularities that can stop a robot from operating, and then usually need a technician’s intervention to resolve. For example, a 6 DoF robot arm, which refers to the six mechanical degrees of freedom of movement of a rigid body in three-dimensional space, can jam. In other words, the robot end-effector becomes blocked in certain directions, and such a blockage is called a singularity.
“Singularities are the Achilles’ heel for industrial robots,” Jacobi notes. “In repetitive tasks, where the robot follows the same motions repeatedly and blindly, robots can be programmed to avoid singularities through weeks of tedious manual fine-tuning of robot paths.
As stated above: “Jacobi says its AI-driven solution promises to cut that time down to a day and can compute motions in less than a millisecond.”
That’s more than significant when trying to sell into a $400 billion global marketplace where speed, productivity, and faultless operation are must-haves for every customer.
If Jacobi’s AI-converged solution can upend the singularity problem, then it may indeed set the future standard for loading the ubiquitous 40” (1 m) x 48” (1.2 m) pallets.